Zero Harm
We prioritize safety globally through our Zero Harm standards and our commitment to continuous improvement. Safety is embedded in our corporate culture, and we work diligently 24/7 to ensure the protection of our people and those who use or interact with our products. Our Global Code of Business Conduct guides our actions to ensure we do the right thing by acting ethically, fairly, and with integrity.Committing to a Zero Harm culture
Zero Harm reflects our conviction that every incident is preventable through changing behaviors. We address Zero Harm through a focus on safe people, safe spaces, and safe systems.
Safe people
• SafeStart: A behavioral-based safety awareness and skills development system • Rate Your State: A peer-to-peer program to build & sustain safety-minded behaviors • Safety observations and accident reporting shared with all regions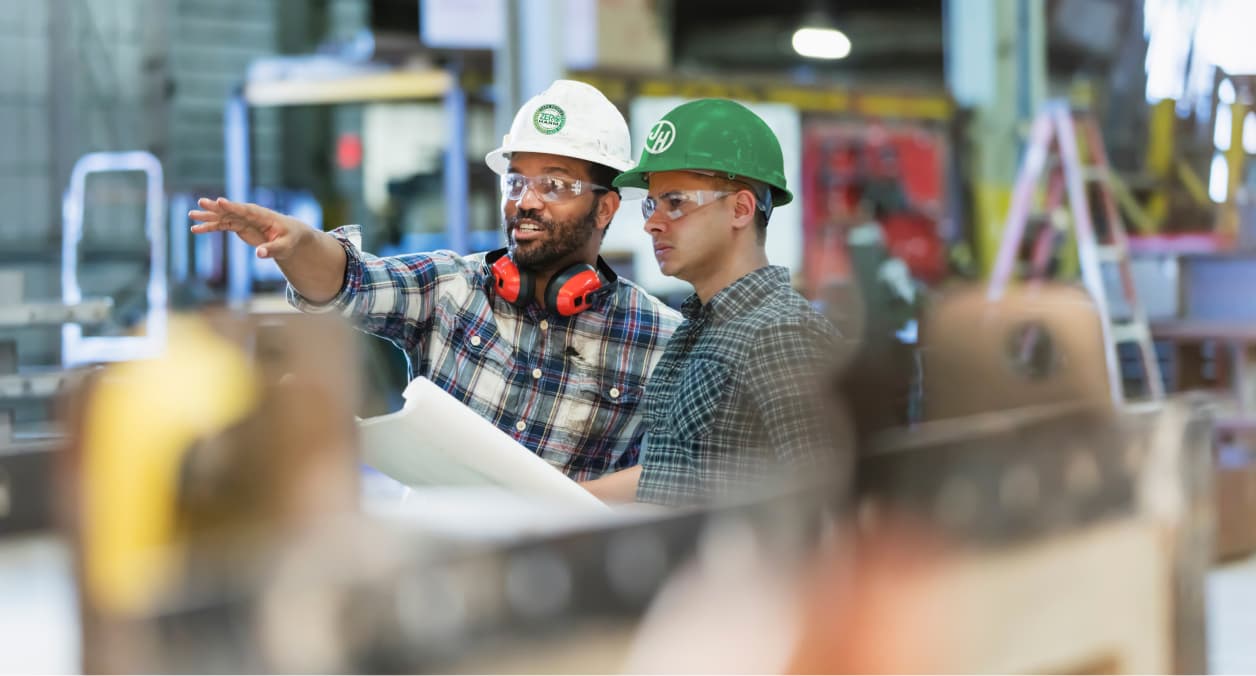
Safe spaces
• Clearly defined responsibilities and authority to stop work for safety concerns • Visual management tools to clearly communicate and simplify processes • Standardized global signage and color coding to easily identify safety risks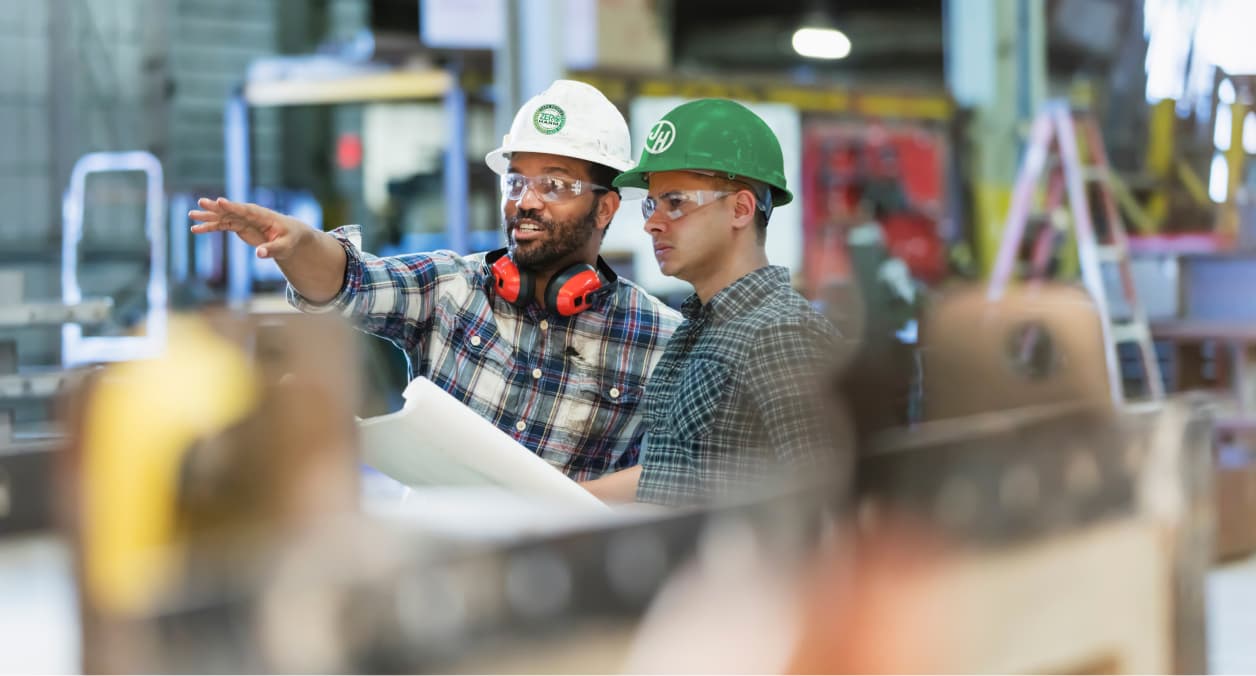
Safe systems
• Hardie Manufacturing Operating System (HMOS) to discuss concerns and solutions • Annual audits and reviews to inform improvement around critical safety risks • Safety Steering Committees and weekly safety meetings at global, regional and local levels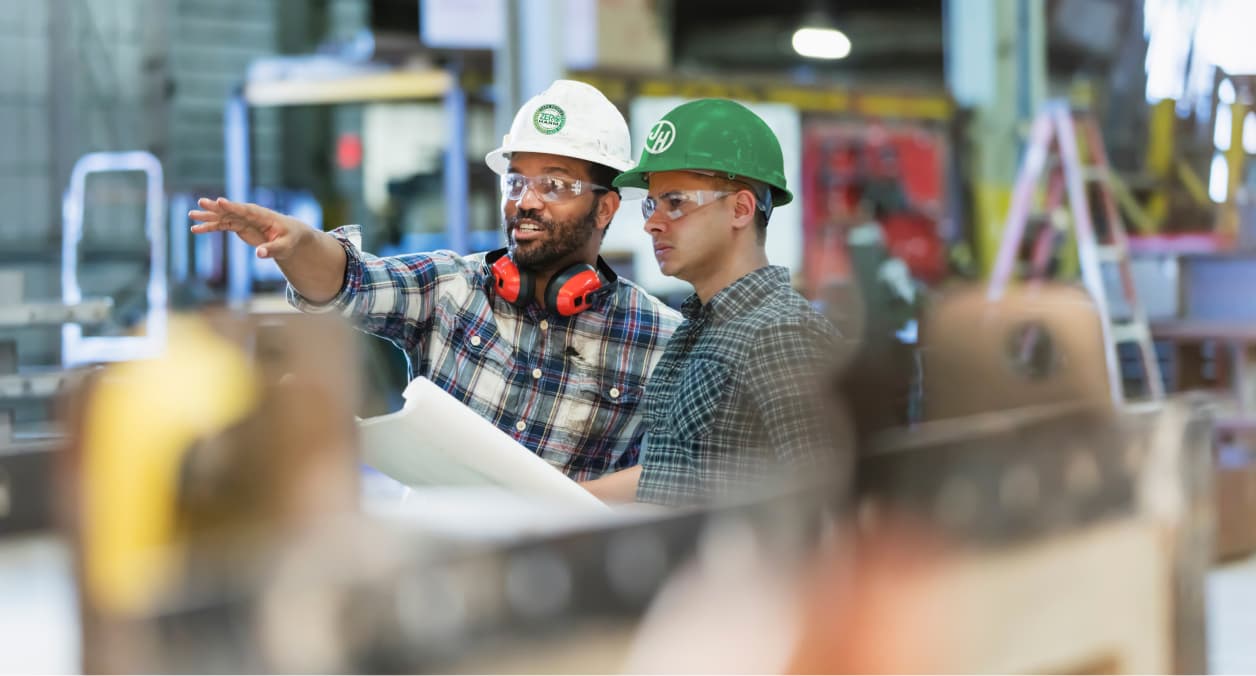
CONTINUOUS IMPROVEMENT
Tracking safety performance
In FY24, we reduced our global DART (Days away from work, restricted work activity or job transfer) rate. In North America, we added new equipment lockouts and other safety equipment, focusing on the interface between workers and machines. In Asia Pacific, we held stop events to encourage conversations after experiencing an incident. In Europe, we invested in training and increased awareness, recording an 80% reduction in the DART rate since FY19, when James Hardie purchased fermacell®.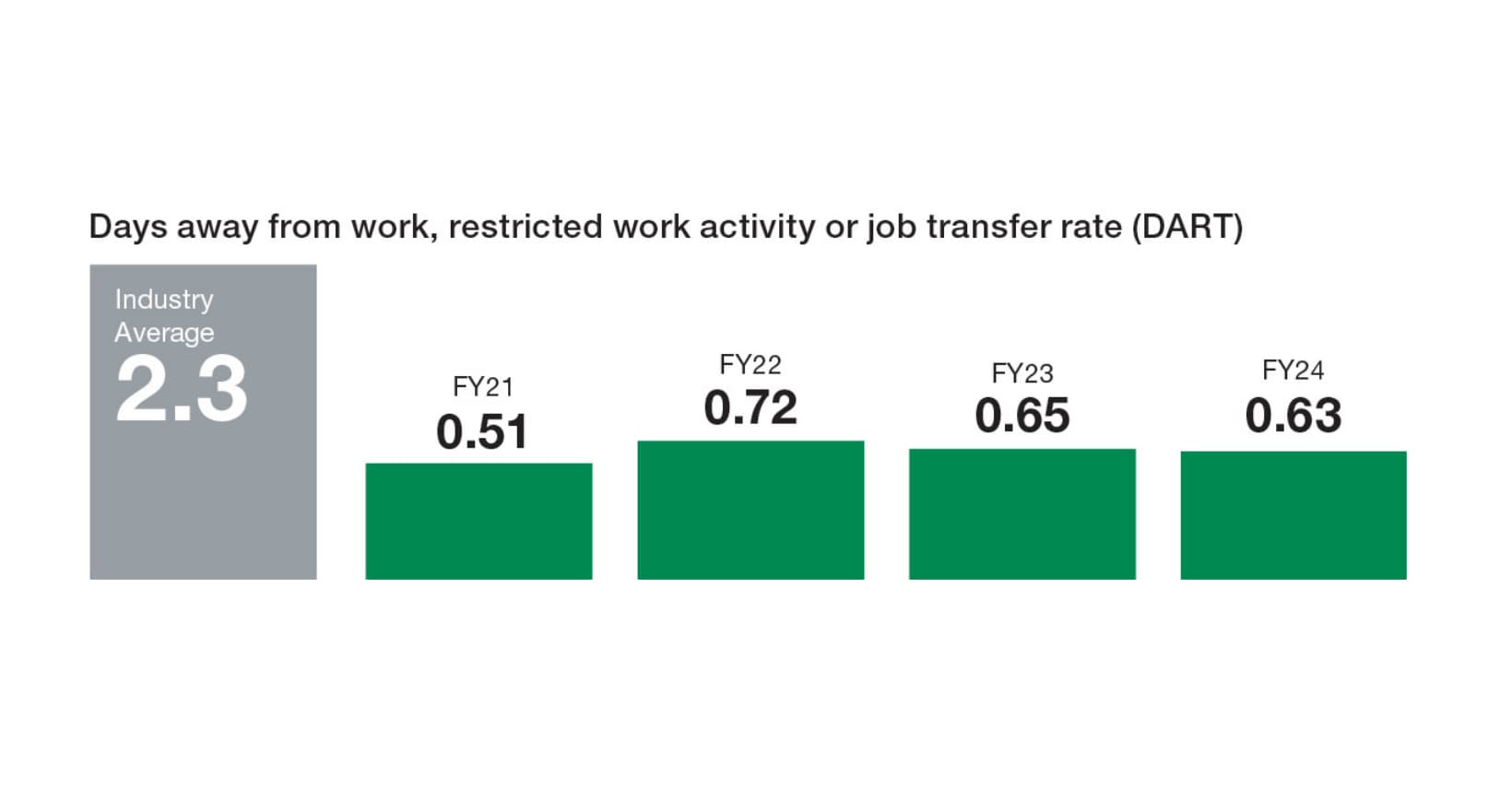
SUSTAINABILITY IN ACTION